Basic Understanding of Solar Panle
Quality Solar Panels
With hundreds of different solar panels on the market it is difficult for those not in the industry to identify quality panels which will perform over the expected 25 year life of a solar photovoltaic (PV) system. Here we highlight the best quality solar panel manufacturers using the latest solar cell innovations to develop the most efficient and reliable panels with the longest life and highest power output.
What is a Tier 1 Solar Panel?
A common term that sales companies and manufacturers use is the 'Tier 1' rating. The Tier rating was developed by Bloomberg New Energy Finance Corporation and is basically used to rate solar panel manufacturers in terms of financial stability. Unfortunately a Tier 1 ranking does not mean a panel offers the highest performance or quality. With most established panel manufacturers now rated as Tier 1, it is more important than ever to know how to distinguish a high quality and reliable panel by other means which we explain in more detail in our solar panel quality review.
Join the discussion about the best solar panels on the solar forum.
Top 10 Solar Panels - Global Ranking
Based on our international rankings, below is the list of the best solar panel manfacturers rated according to quality, reliability, performance, warranty and service, along with feedback from solar industry professionals. See our detailed solar panel quality review here.
Make | Headquarters | Manufactured | Max Eff%** | Warranty* | |
---|---|---|---|---|---|
1 | LG | Sth Korea | Sth Korea, USA | 21.7% | 25 yr |
2 | Sunpower | USA | USA, Mexico, China, Philippines | 22.6% | 25 yr |
3 | REC | Norway | Singapore | 21.7% | 20 yr |
4 | Solaria | USA | Sth Korea, USA | 20.5% | 25 yr |
5 | Panasonic | Japan | Japan, USA | 20.3% | 25 yr |
6 | Qcells | Sth Korea | Sth Korea, China, USA | 20.1% | 25 yr |
7 | JinkoSolar | China | China, USA | 20.4% | 12 yr |
8 | Trina Solar | China | China, Vietnam | 20.5% | 12 yr |
9 | Canadian Solar | China | Canada, China, Vietnam | 20.3% | 12 yr |
10 | LONGi Solar | China | China, India, Malaysia | 20.6% | 12 yr |
* Maximum product warranty period - May vary by country or region
** Maximum solar panel efficiency
Latest update - June 2020
Top 10 Solar Panels - Australia
In Australia, SunPower, LG, REC, Qcells and Winaico are generally regarded the best quality solar panel manufacturers offering the best service, longest warranties, highest efficiency and lowest degradation over the life of the panel. Tindo Solar is the only Australian manufacture and although supply is limited, they are well regarded for producing high quality, reliable solar panels.
There are several other highly regarded panel manufacturers popular in the US, Japan, and across the world which are either not available, have limited supply or are very new to Australia. Here is a short list of some other well regarded solar panel manufacturers.
Have your say - Professional feedback
In addition to continuous feedback from our solar specialists in Australia, the US and around the world, the clean energy reviews team invite all solar industry professionals and installers to give your feedback (positive or negative) from experience with any solar modules or manufacturers.
Latest Solar PV Cell Technology
Here we highlight many of the latest solar panel and PV cell technologies offered by the leading manufacturers. Plus we list some of the more popular panels available on the market using these innovative features.
Most panel manufacturers offer a range of models including mono and poly crystalline (also known as multicrystalline) varieties with various power ratings and warranty conditions. Solar panel efficiency has increased substantially over the last few years due to many advances in PV cell technology including:
PERC - Passivated Emitter Rear Cell
Bifacial - Dual sided panels and cells
Multi Busbar - Multi ribbon and wire busbars
Split cells - half-cut and 1/3 cut cells
Shingled Cells - Overlapping cells
IBC - Interdigitated Back Contact cells
HJT - Heterojunction cells
Dual Glass - Frameless double glass
The eight main solar panel types which utilize one or more of the latest solar PV cell technologies.
These innovations and more explained in detail below offer various efficiency improvements, shade tolerance and increased reliability, with many manufacturers offering up to 25 year product warranties, and 25-30 year performance warranties. However, with all the new panel varieties available it is worth doing some research before you invest in a solar installation. In our complete solar panel review article we explain how to select a reliable solar panel and further highlight the best quality manufacturers on the market.
Solar Panel Efficiency
Solar panel efficiency is one of several important factors to consider and is dependent on both the PV cell type and cell configuration. Average panel efficiency has increased considerably over recent years from around 15% to almost 20% as manufacturers implement the latest cell technologies and innovations. See more details in the complete review of the most efficient solar panels available.
Poly Vs Mono Vs Cast-Mono Cells
The debate is well and truly over. Monocrystalline is the superior cell technology between monocrystalline and polycrystalline silicon cells. Monocrystalline cells (mono) are more efficient as they are cut from a single pure crystal ingot. In the past, the higher cost of mono cells lead the way for polycrystalline technology to become the preferred cell type used. However, over the last few years the cost of mono wafers dropped significantly and most manufacturers have now shifted back to using either mono or cast-mono cells.
Polycrystalline cells, often referred to as multicrystalline or 'multi' cells, are usually made from cast square ingots grown from multifaceted crystalline material (grown in multiple directions). This is cheaper to produce but offers slightly lower efficiency due to the recombination loss which occurs at the grain boundaries. Poly cells are still widely used and very reliable, but as explained below, monocrystalline cells are considered superior due to the higher efficiency and lower temperature coefficient.
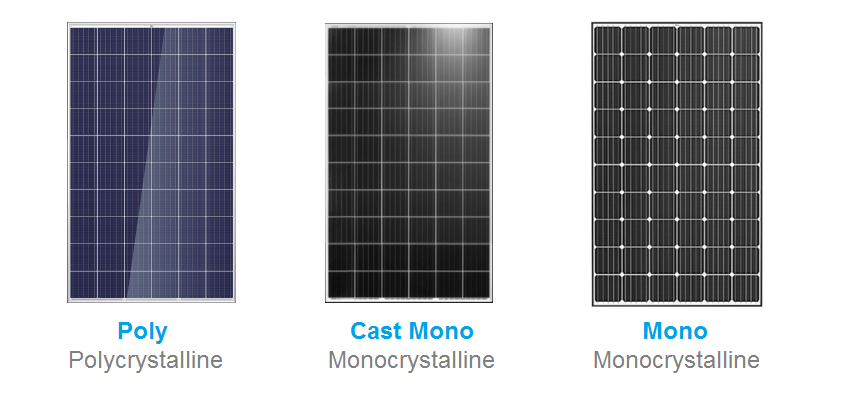
Monocrystalline cells are generally dark black in colour with diamond pattern, while poly or multicrystalline cells are square edged, appear blue in colour. Cast mono are black with square edge much like poly cells.
Cast mono cells
Cast mono cells also known as Quasi monosilicon cells are made using a cast manufacturing process similar to polycrystalline cells. The less energy intensive casting process reduces the cost of manufacturing the ‘mono like’ cells compared to conventional mono cells made using the common Czochralski process. Cast-mono wafers are less susceptible boron-oxygen defects and have a low rate of light-induced degradation (LID) making them comparable in performance and reliability to monocrystalline cells. Cast mono cells have been around for many years but only recently adopted by several of the large panel manufacturers including Canadian Solar, Jinko Solar & GCL.
Why are Monocrystalline cells more efficient?
The inherent benefits of monocrystalline silicon are due to the uniform crystalline structure free of grain boundaries and lower impurities through the unique czochralski manufacturing process. Mono cells have a lower rate of light induced degradation (LID) and also a slightly better temperature coefficient as explained in detail below. In comparison, poly or multicrystalline cells have very small but defined crystal boundaries which can act as minute barriers and reduce efficiency. Mutlicrystalline cells while generally very reliable and long lasting, can be more susceptible to forming micro-cracks after many years of use.
High Temperature Performance
Monocrystalline cells have a slightly lower cell temperature coefficient which results in slightly higher performance in elevated temperature. The power temperature coefficient is the amount of power loss as cell temperature increases. All solar cells and panels are rated using standard test conditions (STC - measured at 25°C) and slowly reduce power output as cell temperature increases. Generally cell temperature is 20-35°C higher than the ambient air temperature which equates to a 8-14% reduction in power output.
Power temperature coefficient comparison - Lower is more efficient
Polycrystalline cells - 0.4 to 0.43 % /°C
Monocrystalline cells - 0.35 to 0.40 % /°C
Monocrystalline IBC cells - 0.29 to 0.31 % /°C
Monocrystalline HJT cells - 0.25 to 0.27 % /°C
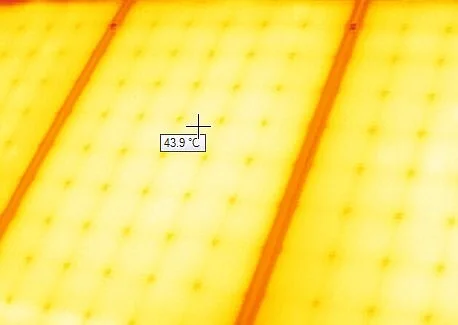
Thermal infrared image of a solar array
The monocrystalline IBC cells described in more detail below have a much lower temperature coefficient of -0.30% per°C. By far the best performing cells at elevated temperatures are the HJC cells from Panasonic and REC which we describe in the last section of this article.
PERC - Passivated Cells
Over the last few years PERC has emerged as the preferred technology for many manufacturers in both mono and poly crystalline cells. PERC stands for 'Passivated Emitter and Rear Cell' which is a more advanced cell architecture using additional layers on the rear side of the cell to absorb more light photons and increase total 'quantum efficiency'. A common PERC technology is the local Al-BSF or local Aluminium Back Surface Field (see diagram below). However, several other variations have been developed such as PERT (passivated emitter rear totally diffused) and PERL (Passivated Emitter and Rear Locally-diffused).
The director of the Australian Centre for Advanced Photovoltaics at UNSW, Professor Martin Green invented the PERC concept which is now widely used by most solar panel manufacturers around the world.

The PERC rear layer local AI-BSF (Aluminium Back Surface Field) used by Trina Solar
Q cells were the first in incorporate PERC technology into mulitcrystalline cells but use the name Q.antum for their range of PERC modules. Jinko solar recently broke the solar efficiency record with 24.79% recorded from a monocrystalline N-type PERC cell. Mono PERC cells are now the most popular and efficient cell type with most manufacturers including Winaico, Trina Solar, Q cells, LONGi Solar, Jinko Solar, Risen and JA Solar now all using PERC cell architecture.
Multiple / Wire Busbars - MBB
Small silver metallic fingers across each cell transfer current to the busbars. More recently, many manufacturers have moved from traditional ribbon busbars to multiple-wire busbars or MBB.
Busbars are thin wires or ribbons which run down each cell and carry the electrons (current) through the solar panel. As PV cells have become more efficient they in turn generate more current and over recent years most manufacturers have moved from 3 busbars to 5 or 6 busbars. Several manufactures such as LG energy, REC, Trina Solar, and Canadian Solar have gone one step further and developed multi-busbar (MBB) systems using up to 12 or 16 very thin round wires rather than flat busbars. The problem with traditional flat ribbon busbars is they shade part of the cell which slightly reduces performance, hence why they must be carefully designed. On the other hand multiple round wire busbars provide lower resistance and a shorter path for the electrons to travel along the fingers, resulting in higher performance.
If a cell micro-crack occurs due to impact, heavy loads or people walking on panels, more busbars help reduce the chance of the crack/s developing into a hot spot as they provide alternative paths for current to flow.
LG Neon 2 cells with 12 round wire busbars.
The LG Neon 2 modules where the first to use 12 small round wire busbars which LG refer to as 'Cello' technology which stands for 'cell connection, electrically low loss, low stress and optical absorption enhancement'. It's a bit of a mouth full but basically the Cello multi-wire technology lowers electrical resistance and further increases efficiency.
Multi-busbar compared to a standard ribbon busbar - Image credit Trina Solar (click to enlarge)
Trina solar along with many other manufacturers recently started offering thin round wire busbar cells under the name multi busbar (MBB) as an option on a range of modules in 2019. As explained earlier, another benefit of having more busbars is if micro-cracking does occur in a cell due to external stresses there is less chance of this forming a hotspot as the electrons have many alternative busbars to flow along. This is shown in the diagram opposite.
See the complete Trina Solar panel and technology review here
Split Modules With Half-Cut Cells
Most of the world’s leading manufacturer’s have now shifted to half-cut or half size cells rather than traditional full size square cells. This effectively splits the solar panel into two smaller panels of 50% capacity which work in parallel. This has multiple benefits including increased performance due to lower resistive losses through the bus bars (current collectors). More recently, a number of manufacturers such as Trina Solar began producing extra-large 210mm square cells which enable the cell to be cut into three sections, known as 1/3-cut cells. These large format cells are used to produce high-powered panels up to 600W.
Since each cell is half size, it produces half the current at the same voltage, which means the width of the busbar can be reduced by half in turn reducing cell shading, losses and increasing efficiency. The lower current also translates to lower cell temperatures which in turn reduces the potential formation and severity of hot spots due to localised shading, dirt or cell damage. In addition, the shorter wire distance to the center of the panel from the top and bottom further boosts efficiency and can increase power output of a similar sized panel by up to 20W.
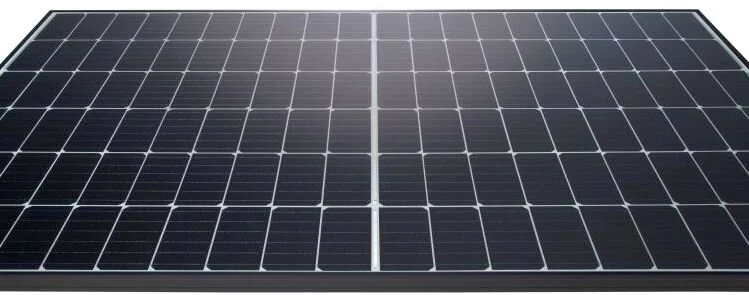
The Hanwha Q Cells Q.Peak Duo G6 panel uses half cut mono PERC cells with 6 round wire busbars
Improved shade tolerance
Another substantial benefit is that partial shading on either the upper or lower part of the panel does not reduce the power output of the panel the same amount as a panel with conventional full size cells. This is due to the upper and lower sections being connected in parallel and acting much like smaller individual panels. During partial shading, the voltage is maintained and current loss is reduced by 50%, meaning better performance when shaded.
REC Twin Peak panels were some of the first available with half-cut cells (click to enlarge)
The REC twin peak 2 range of split panels have been available for some time and now most majar panel manufacturers are following suit with split panels being released by Trina Solar, Q-cells, Canadian Solar, LONGi Solar, JA Solar, Risen, Phono solar, Jinko solar and most other manufacturers.
BiFacial Solar Modules

Rear side of a LG Neon 2 bifacial module
Bifacial solar technology has been available for several years but is starting to become popular as the cost to manufacture the very high quality monocrystalline cells required continues to decrease. Bifacial cells absorb light from both sides of the panel and in the right location and conditions can produce up to 27% more energy than traditional monofacial panels. Bifacial solar panels typically use a glass front and clear rear polymer backsheet to encapsulate the cells which allows reflected light to enter from the rear side of the panel. Bifacial modules can also use a glass rear side which lasts longer and can significantly reduce the risk of failure, with some manufacturers now offering 30 year performance warranties on bifacial panel models.
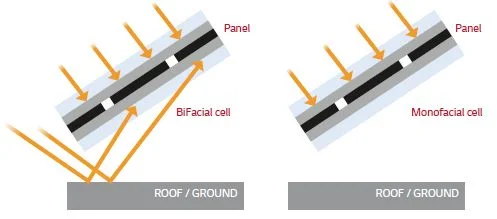
Bifacial solar modules also absorb reflected light energy on the rear side of the cells - Image credit LG energy
Traditionally bi-facial solar panels were only used in ground mounted installations in unique locations where the sunlight is easily bounced or reflected off the surrounding surfaces, in particular snow-prone regions and extreme latitudes. Although they have been proven to work well when ground mounted over light sandy surfaces and are also able to achieve up to 10% higher output even on light coloured rooftops when tilted. Manufacturers producing bifacial solar panels include LG energy, Trina solar, Jinko Solar and Yingli Solar.
Dual Glass Panels
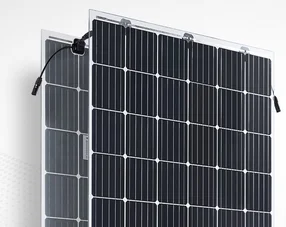
LONGi solar dual glass panels with 30yr warranty
Many manufacturers are now producing what is known as glass-glass, dual glass or double glass solar panels which should not be confused with bifacial technology. The rear glass replaces the traditional white EVA (plastic) backsheet and creates a glass-glass sandwich which is considered superior as glass is very stable, non reactive and does not deteriorate over time or suffer from UV degradation. Due to the longer life of glass-glass panels some manufacturers such as Trina solar are now offering 30 year performance warranties.
Frameless Panels
Many double glass panels are also frameless having no aluminium frame which can complicate the mounting of panels as special clamping systems are required. However, frameless modules offer several advantages especially in regards to cleaning, with no frame to catch dirt and dust the frameless modules when tilted or flat are much easier to clean and are more inclined to aid from wind and rain to self-clean which results in greater solar output. However without the strength of an aluminium frame double glass panels, although more durable, are not as stiff and can appear to flex or bow, especially when mounted flat or horizontal.
Manufacturers producing dual glass solar panels include Jinko solar, LONGi Solar, Trina Solar, Yingli Solar and JA solar.
Smart Panels And Power Optimisers

The add-on Tigo DC power optimiser
A technology which is becoming more popular is the addition of DC power optimisers within the solar panel. Optimisers along with micro-inverters are generally known as MLPE or Module Level Power Electronics, which as the name suggests consists of small power conversion units attached directly to individual solar panels. DC Optimisers are designed to supply the optimum voltage for maximum power generation. If a panel is shaded, dirty or under performing resulting in low voltage or current, optimisers can compensate for the poor performing panel to provide the optimum voltage to the inverter.
Power optimisers are available from Tigo, SolarEdge and more recently Huawei. Both SolarEdge and Tigo have developed panels with inbuilt optimisers at the junction box on the rear side of the panel. SolarEdge differs to Tigo and Huawei in that the SolarEdge optimisers must be used together with the SolarEdge inverters, while the Tigo and Huawei optimisers can be be attached to any existing panels as an add-on optimiser. See full Tigo optimiser details here.

SolarEdge DC Power Optimisers
A big advantage of 'add-on' optimisers such as those from Tigo and SolarEdge is the ability to monitor the performance of each solar panel individually, this can also help highlight any faults and issues in a solar array. Micro-Inverters also offer this advantage over common string inverters.
Maxim Integrated went one step further and developed submodule optimiser chips. These smart chips from Maxim go beyond the traditional add-on optimiser and separate the panel into 3 strings of cells which enables the panel to operate at the optimum MPPT voltage when partially shaded or dirty. It is worth noting that some installers have reported customers having RFI interference issues (TV & radio) using this new technology however the next generation Maxim chips are claimed to have resolved the RFI problem.
Shingled Cells
SunPower P series Shingled solar cell construction - Image credit Sunpower
Shingled cells are an emerging technology which use overlapping thin cell strips that can be assembled either horizontally or vertically across the panel. Shingled cell are made by laser cutting a normal full size cell in to 5 or 6 strips and layering them in a shingle configuration using rear side connection adhesive. The slight overlap of each cell strip hides a single busbar which interconnects the cell strips. This unique design covers more of the panel surface area as it doesn’t require front side busbar connections which partially shade the cell, thus increaseing the panel efficiency much like IBC cells explained below.

Seraphrim Eclipse uses the horizontal shingled cell format.
Another benefit is that the long shingled cells are usually connected in parallel which greatly reduces the effects of shading with each long cell effectively working independently. Also shingled cells are relatively cheap to manufacture so they can be a very cost effective high performance option, especially if partial shading is an issue.
Seraphim were one of the first manufacturers to release shingled cell modules with there high performance Eclipse range of panels. The SunPower P series are a more recent addition to the SunPower range offering a lower cost option primarily for large scale applications. Other manufacturers producing shingled cell solar panels include Yingli Solar and Znshine.
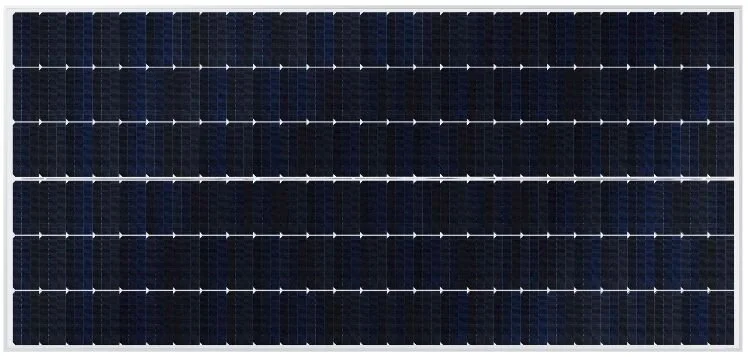
SunPower P19 series panels use the verticle shingled cell format to achieve up to 415Wp.
Panel And Cell Strength
Along with the many cell advancements to improve efficiency there are also new technologies to increase reliability and performance over the expected 25 year life of a solar module. Solar panels can be put under extreme stress due to wind lift forces, vibrations, extreme heat and freezing cold causing expansion and contraction. These can develop micro-cracks, hot spots and PID (potential induced degradation) within the cells leading to reduced performance and accelerated failure.
Manufacturers such as Winaico and LG, and the Q.Peak DUO panels from Qcells have extremely strong aluminium frames to help reduce cell and module stresses in high wind locations that experience cyclonic weather.
IBC cells - High strength and durability
IBC silicon cells explained in detail below are not only more efficient but also much stronger than conventional cells as the rear layers reinforce the whole cell and help prevent micro-cracking which can eventually lead to failure.
Sunpower use a high grade solid copper IBC rear foundation layer on their patented 'Maxeon' cell design along with a highly reflective metal mirror like surface to reflect any light which passes through back into the cell. The rear side of the 'Maxeon' IBC cell shown below is extremely tolerant to stress and bending unlike conventional cells which are relatively brittle in comparison.
The rear side of a Sunpower 'Maxeon' IBC cell showing the fine metal grid conductors which improves efficiency, helps reinforce the cell and prevents micro-cracking.
High Efficiency N-Type Solar Cells
While PERC and bifacial are the talk of the solar world the most efficient and reliable technology is still the N-type monocrystalline cell. The first type of solar cell developed in 1954 by Bell labs used an N-type doped silicon wafer but over time the more cost effective P-type silicon became the dominant cell type with over 80% of the global market in 2017 using P-type cells. With high volume and low cost being the main driving factor behind P-type it is expected that N-type will become more popular as the manufacturing costs reduce further and efficiency increases.
SunPower IBC N-type cells with solid copper backing achieve ultra-high efficiencies over 22% - Image credit Sunpower Corp
IBC Cell Technology
IBC or Interdigitated Back Contact cells have a grid of 30 or more conductors integrated into the rear side of the cell, unlike standard cells which typically have 4 to 6 large visible ribbon busbars and multiple fingers on the front side of the cell. The most obvious problem with the more common front exposed busbar design is they partially shade the cell and reflect some of the light photons which reduces efficiency, while IBC cells don't suffer this problem and as a bonus look much 'cleaner' with no exposed busbars.
The most efficient solar panels - IBC N-type
The world's most efficient and best performing solar panels are manufactured by SunPower and LG using IBC N-type monocrystalline silicon cells and although they are the most expensive, they are without doubt the most reliable and highest quality panels available.
The complete list of the most efficient solar panels in 2020.
For many the higher cost of the these premium N-type solar panels ($1 or more per W) is outweighed by the higher efficiency which ranges from 20 to 22.6%, improved performance at higher temperatures and minimal light induced degradation (LID), which means much higher energy yield over the life of the panel. The industry leading performance warranty is offered on both the SunPower Maxeon 2 and 3 series panels of up to 92%. The LG Neon R and Neon 2 panels are also covered by a 25 year product warranty and a new minimum 90 to 90.8% performance warranty after 25 years.
Heterojunction - HJT Cells
HJT solar cells use a base of common crystalline silicon with additional thin film layers of amorphous silicon on either side forming what is known as a heterojunction. The different photovoltaic layers absorb light of different wavelengths and thus boost overall cell efficiency. As opposed to the common P-N junction cells, the next-generation heterojunction cells have the potential to dramatically boost increase efficiency with lab testing achieving cell efficiencies up to 26.5% when combined with IBC technology.
Following the early HJT development work at UNSW and Sanyo, Panasonic created the efficient 'HIT' range of panels and were the leaders in HJT cell technology for many years. However, REC group recently released the Alpha series panels which use half-cut HJT cells combined with 16 micro busbars (16BB) to achieve an impressive 21.7% panel efficiency.
Panasonic HiT (HJT) cell construction - Image credit Panasonic Corporation
Panasonic developed the HIT cell using a high performance N-type silicon base to produce panels with an efficiency up to 20.0% and excellent high temperature performance. The N-type silicon cells also offer exceptional long term performance guaranteeing 90.76% output after 25 years, the second highest available behind SunPower. See full specifications – Panasonic HIT N335W.
The unique Panasonic HIT panels are only available in Japan and North America, but unfortunately the are not available in Australia. Considering the high average temperatures in Australia they would be a great choice for rooftops and large scale commercial applications… hint!
HJT cells offer the best high temperature performance

The new REC Alpha series with half-cut HJT cells
The most impressive characteristic of HJT cells is the incredibly low temperature coefficient which is around a 40% improvement over common multi and mono silicon crystalline cells. Solar panel power is rated under Standard Test Conditions (STC) which is measured at a cell temperature of 25°C. Every degree above the STC temperature reduces power output by a small percentage known as the power temperature coefficient. In common multi and mono cells, the temperature coefficient is 0.38% to 0.42% per °C which can add up to reduce total output by up to 20% during very hot windless days. In comparison Panasonic's HIT cells have an very low 0.26%/°C temperature coefficient which is the lowest of any cell manufactured today.
Note: panel and cell temperature is also effected by roof color, tilt angle and wind speed, so mounting panels flat on a very dark rooftop will usually reduce panel performance compared to lighter colored rooftops.
More information
How are solar panels made?
Solar panels are made using a series of PV cells protected by glass, EVA and a protective back sheet housed in a tough aluminium frame. The components must be engineered to withstand years of extreme weather temperatures and high wind forces. Here we explain each component in detail and why it is vital to the long term performance of a solar panel.
Source Credit : https://www.cleanenergyreviews.info/blog/2017/9/11/best-solar-panels-top-modules-review
Comments
Post a Comment